Our mission is to provide the best solution to each problem that might arise, at a fair price, all while building a lasting relationship with our customers.
We want to provide our customers services that give them peace of mind, from the way we service and maintain their refrigeration systems, to our speedy responses on after-hours emergency calls for said systems. We make a commitment to work side-by-side with our customers to provide them with the most efficiently operating system possible.
Our commitment to "Quality" shows in the lasting relationships we build with each one of our customers.
If you would like to contact us, whether it be for service, to simply ask a technical question thats been bothering you, or would like a quote to compare to your current service provider, please fill the contact form on our website, or contact us directly at the number below. We pray God blesses you and yours!
At 1st Quality Refrigeration, we specialize in delivering the highest level of industrial refrigeration service tailored to meet the unique needs of each customer.
Our Services
24 hour emergency service
We all know that the time our systems are going to give us the most problems is just as we get comfortable at home. We here at 1st Quality consider ourselves to be "partners" with our customers. This means that we are equally invested in ensuring that their systems operate as efficiently and effectively as possible at all times, regardless of the time of day or night. Our service technicians are trained to maintain or repair many different types of equipment from a small piece of commercial equipment to the largest industrial system, regardless of the configuration or refrigerant inside of it.
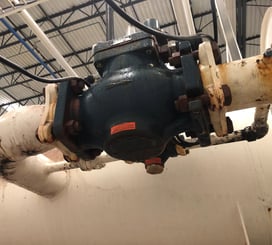
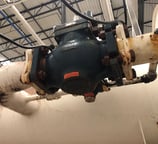
Part Sales / Lubricant / Refrigerant
Don't know what it is but know that it needs to be replaced? Give us a call, we can help! We will work with you to identify what the problem is, what it will take to fix the issue, and will work with one of our many suppliers to make sure that you get exactly what you need, when you need it. We have partnerships with all major manufacturers, as well as companies like AirGas, ISEL, and Camco for all of your lubrication and refrigerant needs.
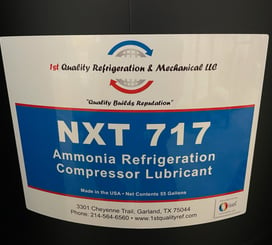
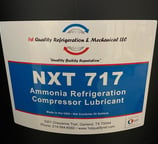
Planned Maintenance Programs
Regardless of how well designed and installed a refrigeration system may be, if it was built by man it's not a matter of "if" but rather "when" a portion of it is going to break down. The difference being in how well the system is maintained after its inital install and startup. We work with the customer to design a custom maintenance program that complies with all manufacturer recommendations for each piece of equipment in an attempt to increase its efficiency, as well as its extending its service life.
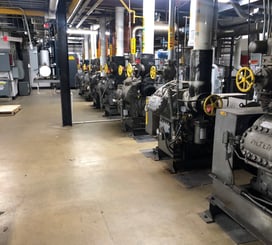
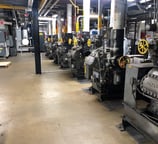
Controls / Automation
This portion of the system is often times the most complex portion of a refrigeration system, thus making it the most difficult part to troubleshoot or repair. Also, with the ever-changing technologies we face, customers are often times left to either leave their control systems as they are, making them more difficult to repair as the parts become obsolete, or bring them up to the newest standards / technology. Whether you are attempting to repair what you have, or are changing to newer technology we can help. We will work with you to make the necessary repairs or figure out how to integrate the most current technology available to your system.
Compressor Rebuilding
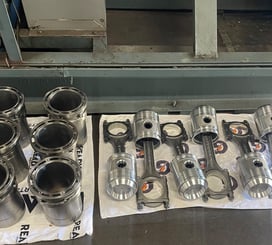
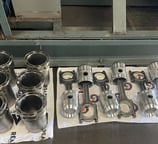
The heart of each and every refrigeration system is the compressor. Without this component the refrigeration cycle does not exist. Often times these machines set back in the engine room, sight-unseen, for days, weeks, or even months. While they are built by the manufacturers to run many hours under normal use and maintenance practices, and are designed to withstand alot of wear and tear, over time the internal components of these machines wear out, and need to be replaced or machined back into normal tolerances. This is where we come in. We will work with you to schedule a time to come in, and depending on the type of compressor you have, will either rebuild the compressor in place, or remove the compressor from its package, load it onto a trailer, and take it back to the shop to be rebuilt. We completely disassemble the machine, clean all of the parts, replace all parts necessary, and have machine work done if necessary and possible. We then reassemble the compressor and verify that all tolerances / clearances are reset to manufacturer's recommendations. If we removed the compressor we then contact you and schedule a time for us to return to your site, re-install the compressor onto its package, perform a start-up on it, and monitor it for proper operation. We log all operating conditions at the time of the start-up, and make recommendations and adjustments necessary to ensure that the compressor is operating within its design specifications.
Address:
2514 Southern Oak Trl
Terrell, Tx. 75161
Phone:
214-564-6560
Email:
office@1stqualityref.com
© 2025 www.1stqualityref.com
TDLR License Number:
TACLA74377C